Manufacturing
Assembled in Style in Kansas City
Ever wonder how your FireBoard was made? You may be surprised to learn that FireBoard assembles their smart thermometers at their headquarters in Kansas City, Missouri. See below for the full rundown on how FireBoard makes their devices.
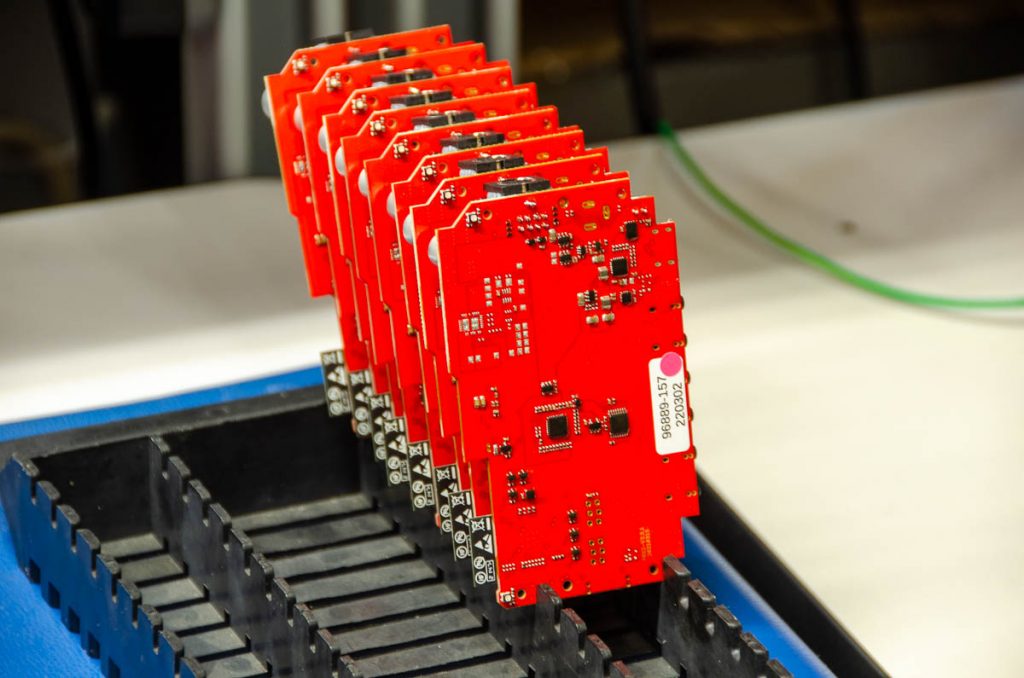
“The red solder mask on our PCBs is a fun way to carry our FireBoard branding to the end product” Ted Conrad, co-founder of FireBoard
FireBoard assembles their own circuit boards, which is a pretty big deal for a technology company. See more about FireBoard’s goals in becoming a vertically integrated company and how their surface mount assembly line makes the boards in a previous post here. And if you are wondering why are their circuit boards are red? Ted Conrad explains “the red solder mask on our PCBs is a fun way to carry our FireBoard branding to the end product” the co-founder of FireBoard goes on to say “it also reflects our attention to quality and detail with our hardware designs.”
Thru-Hole Soldering
After finishing the surface mount assembly line, the boards still require additional components, such as a variety of connection ports or even a vibration motor, which gives the Spark its haptic feedback. These components are thru-hole soldered to the board. While FireBoard has been doing some of this soldering by hand, the company is in the process of adding an automated selective solder machine (and a selective coating machine). Stay tuned for more information as these machines are delivered!
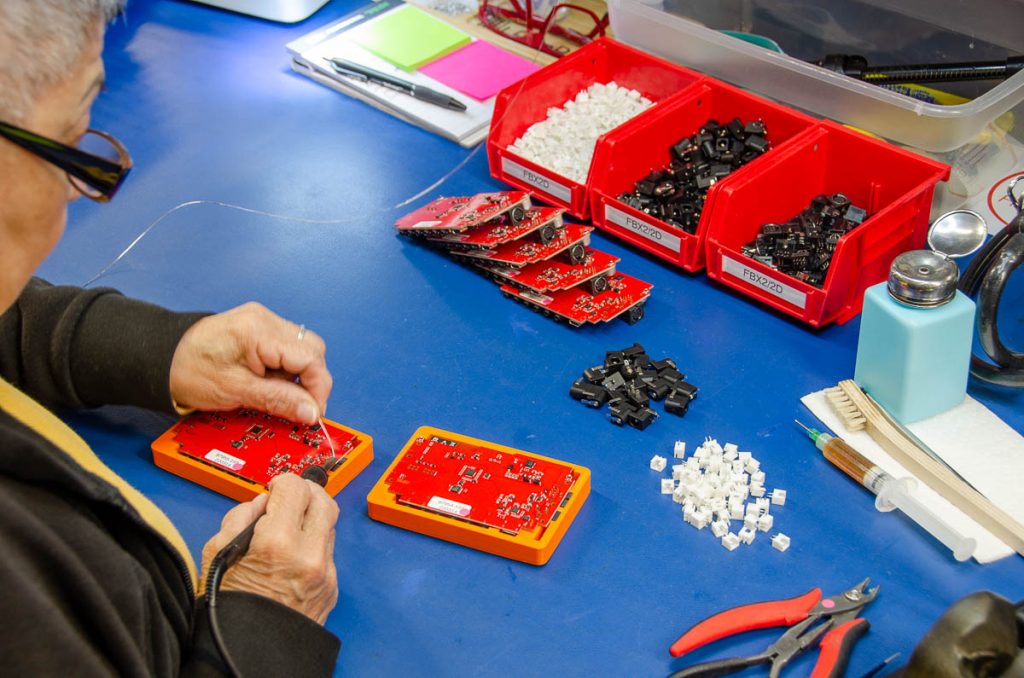
Linda thru-hole soldering components on a FireBoard Drive motherboard
Flashing
Once these components are added, the boards go to the flashing station where the firmware is added to the mother board’s flash memory. They are capable of flashing multiple boards simultaneously.
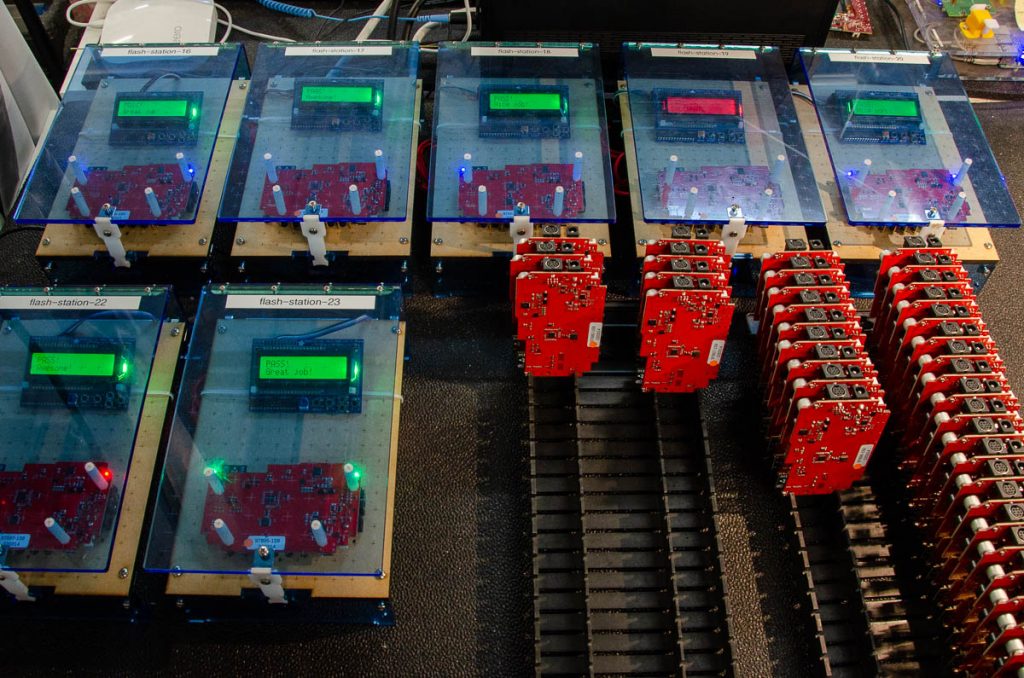
FireBoard motherboards being flashed
Water Resistant Coating
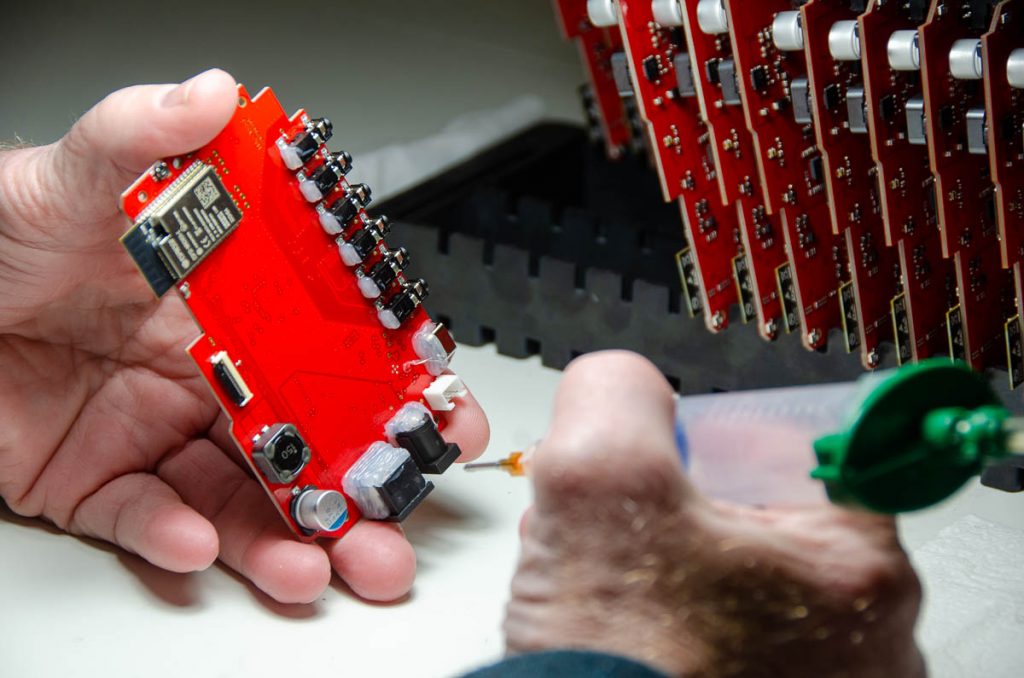
Mike adding a water resistant coating to electrical components
At this phase, the components are treated with a water resistant coating. While not waterproof, it does ensure our products can withstand the occasional splash or rain shower.
Final Assembly
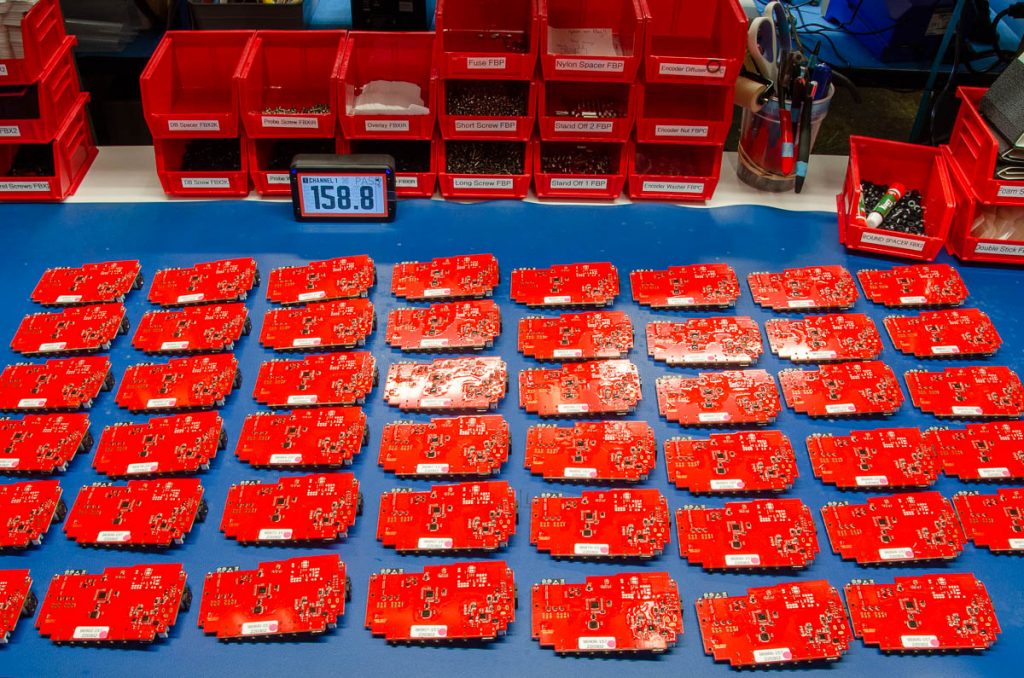
Wendy’s workstation
The final assembly stage is where the FireBoards really comes together. “This is my favorite part of the assembly process,” FireBoard assembly worker Wendy Jones says as she is lining up dozens of circuit boards on her work table. “If everything is going right I can put together 96 boards in a day.” After she attaches the battery and LCD screen to the motherboard, it is then installed into the case, and screen cover is attached. Now the FireBoard is sealed up and is ready for the last step.
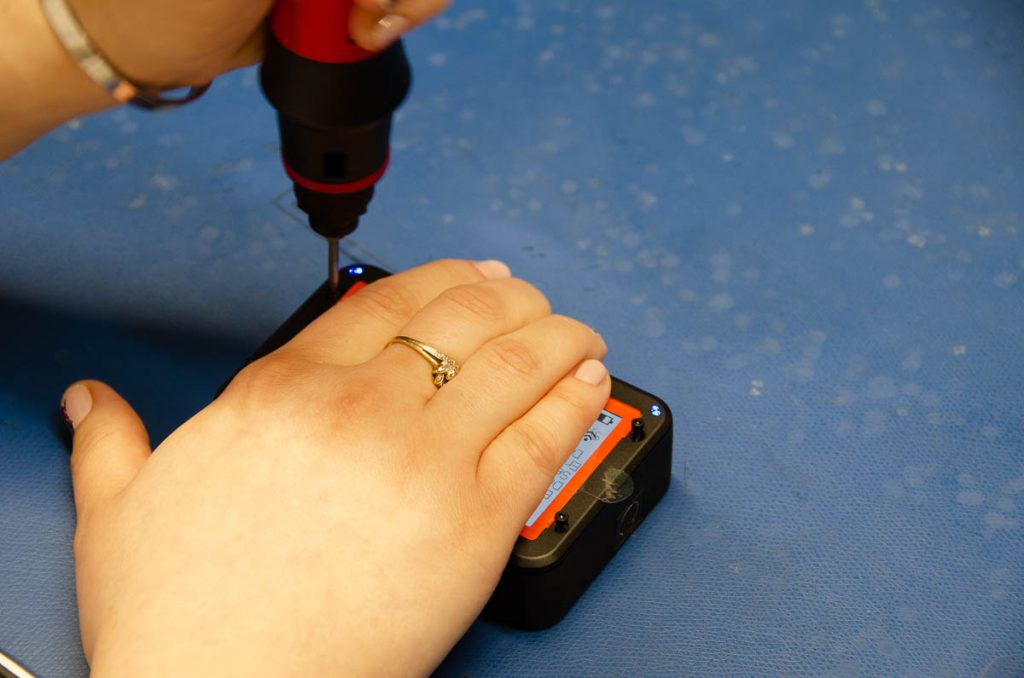
Bezel and screen protector being fastened into place
Final Check
Final Check is a quality control procedure FireBoard puts all of their devices through. First ports and bezels are inspected for proper fit and alignment ensuring the case and components went together properly. Then they run a systems check, testing that buttons, LCD screen, and LEDs are working properly. A finishing touch is the application of a serial number on the case then loading the freshly assembled FireBoards into containers where they await packaging.
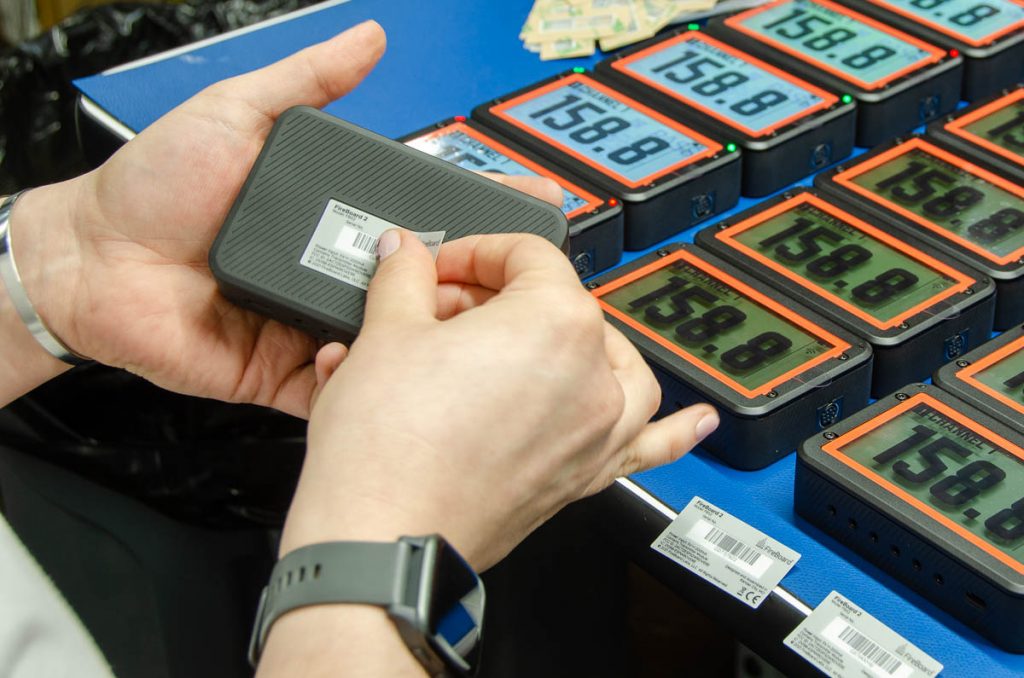
Application of the label with serial number on the back of the case
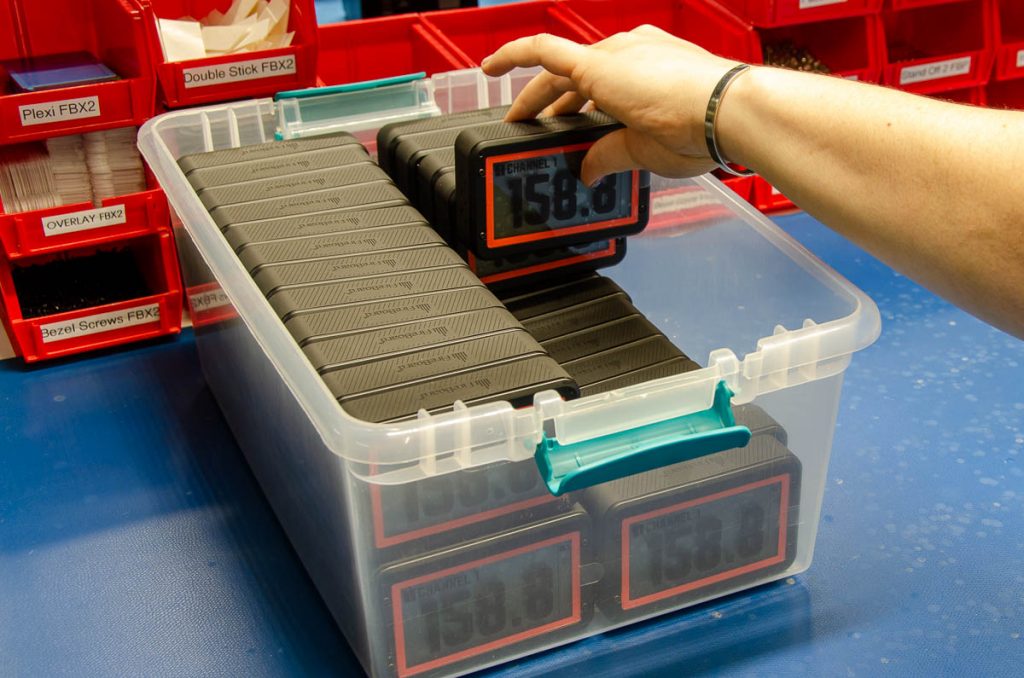
New FireBoard 2 ready for packaging
2 Comments
Trey
Cool post. Always interesting to see how things are made. My FB1 is still working great and I’m sure it went through the same processes. Except I had to buy the case to make it water resistant. Lol. Tell Wendy she’s doing a great job producing 96 boards a day! Keep up the great work!
Patrick Stavros
So the board is assembled in the US. How many of the parts that go into the Fireboard are made in the US?