Manufacturing
Injection Molded Plastics at FireBoard Labs
In an ongoing effort to showcase our in-house manufacturing, we will examine injection molded plastics by looking at the processes behind the design and manufacturing of some of our most common parts. For more information on how we make our products visit any of our blogs in the Manufacturing category of our News tab at FireBoard.com.
How We Are Using Plastics
Common in the consumer electronics market, plastics are ideal for mass production, electrical insulation, and environmental protection. In the case of the FireBoard Spark and FireBoard 2, their case is a single part made from injection molded plastic topped with an aluminum bezel with a clear plastic lens. The FireBoard Beacon sensor is assembled from 3 different injection molded pieces. Using plastics allows for excellent strength-to-weight and texture for a great in-hand feel. In the case of the Spark, the plastic and additional rubber molding of the case aid in attaining its IP66 rating.
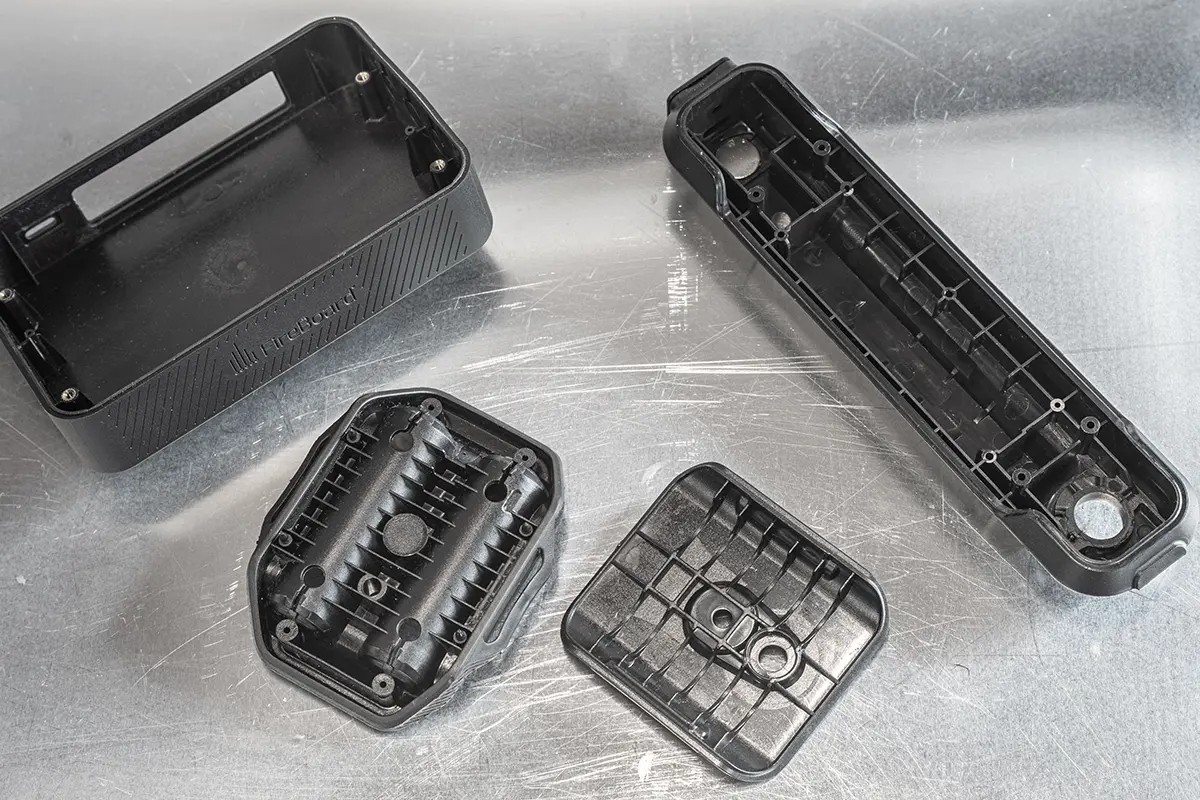
Examples of injection molded cases designed by FireBoard for their range of smart thermometers include (from left to right) the Fireboard 2, Beacon temperature and humidity sensor, and Spark instant-read thermometer.
Tooling
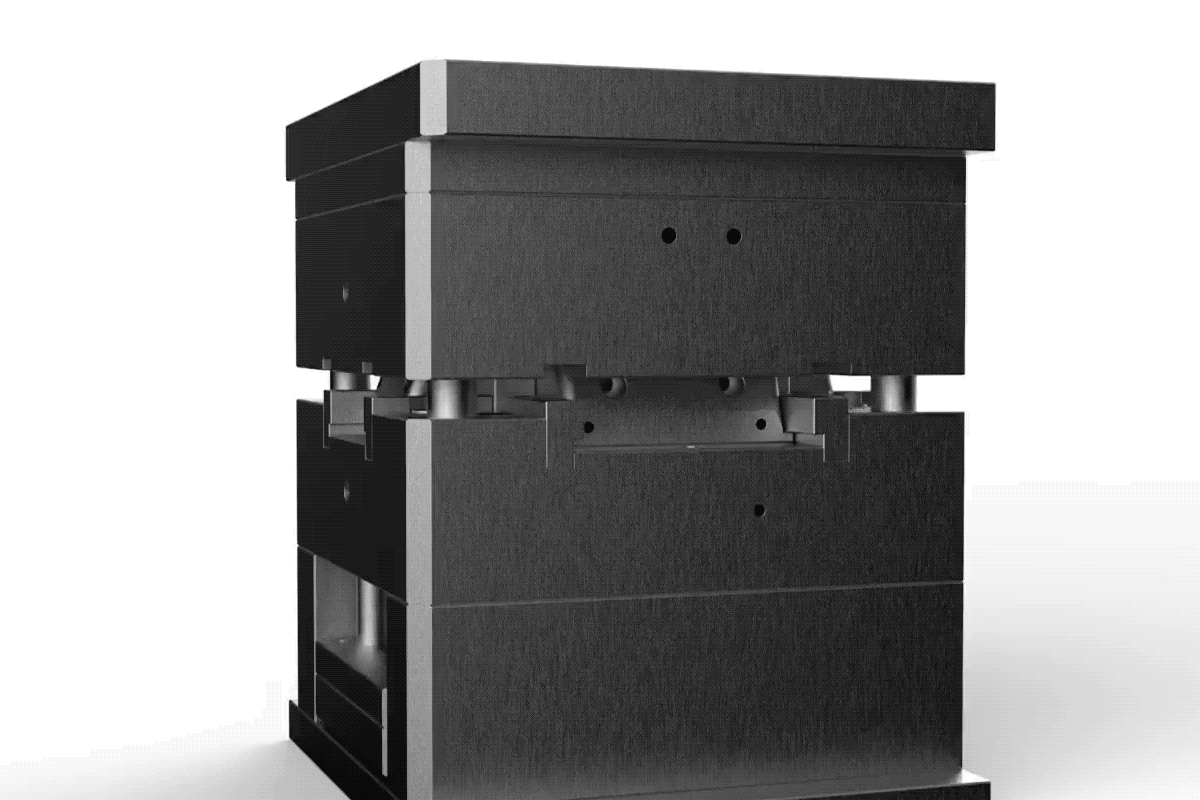
Animation of the tooling at work creating a FireBoard 2 case.
After the initial design work is complete and prototypes have been finalized, the tooling for the molds are made. The molds, or tooling, are cut from solid steel. The moldmaking process is very specialized, and at this point, FireBoard relies on toolmakers to create high precision molds. The toolmakers have various machines on-hand to cut steel including 3-axis and 5-axis CNC mills. Most recently, we have been working with a group using the fascinating process of Electrical Discharge Machining, or EDM for short. EDM is a machining process worthy of its own blog post and is known for producing tooling with precision and detail beyond the capabilities of conventional milling.
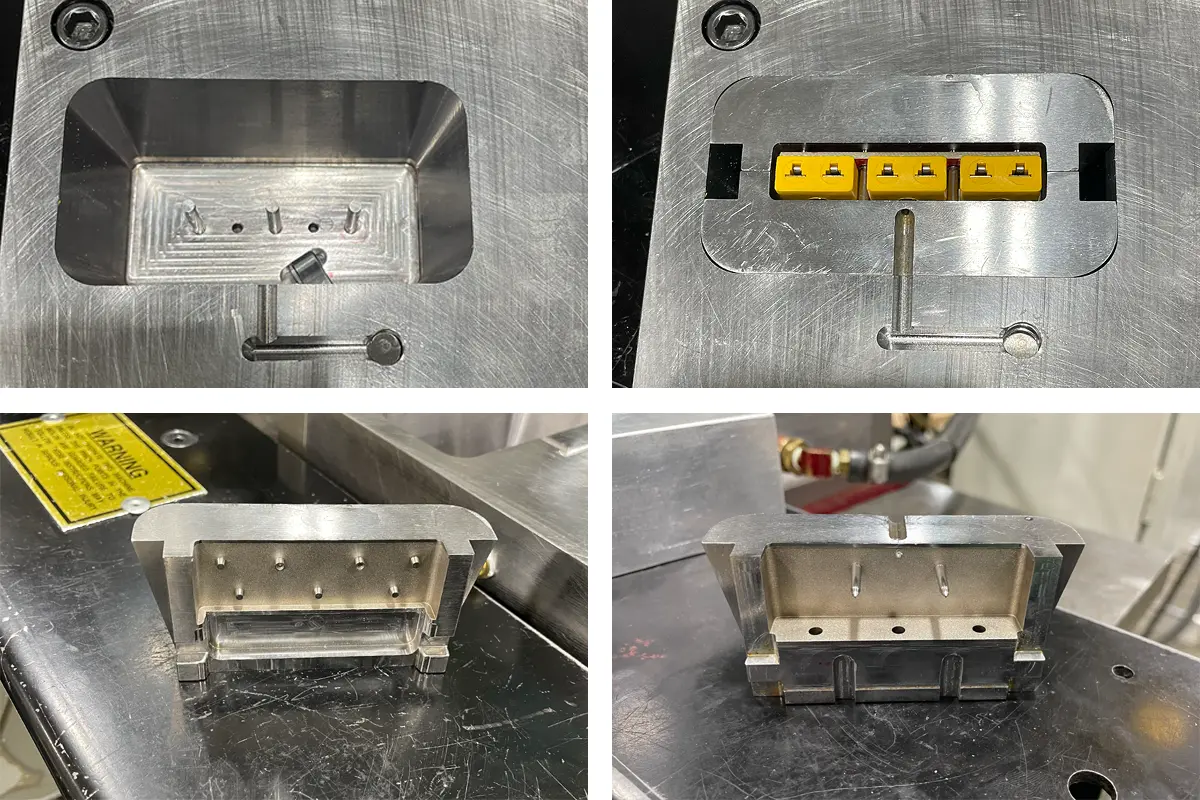
Some of FireBoard’s molds used for injection molded plastic production, including the K-Type plugs for the FireBoard 2 Pro case.
After the Mold is Made
Injection molding involves melting plastic pellets and injecting the molten material into a custom-made mold. Once cooled, the mold is opened and the finished plastic part is ejected. This process is efficient for the mass production of intricate and precise plastic components. Choosing the appropriate plastic material is based on the properties, such as durability, heat resistance, appearance, and texture. Rubber, for example, is often used on the exterior for positive grip.
What follows are a series of photos that illustrate the creation of one of our Drive cables from mold to finished product by Tri-V Tool and Manufacturing in Omaha, NE. We supply Tri-V with a pigtail plug and circuit board, and they finish the product using a process called over-molding.
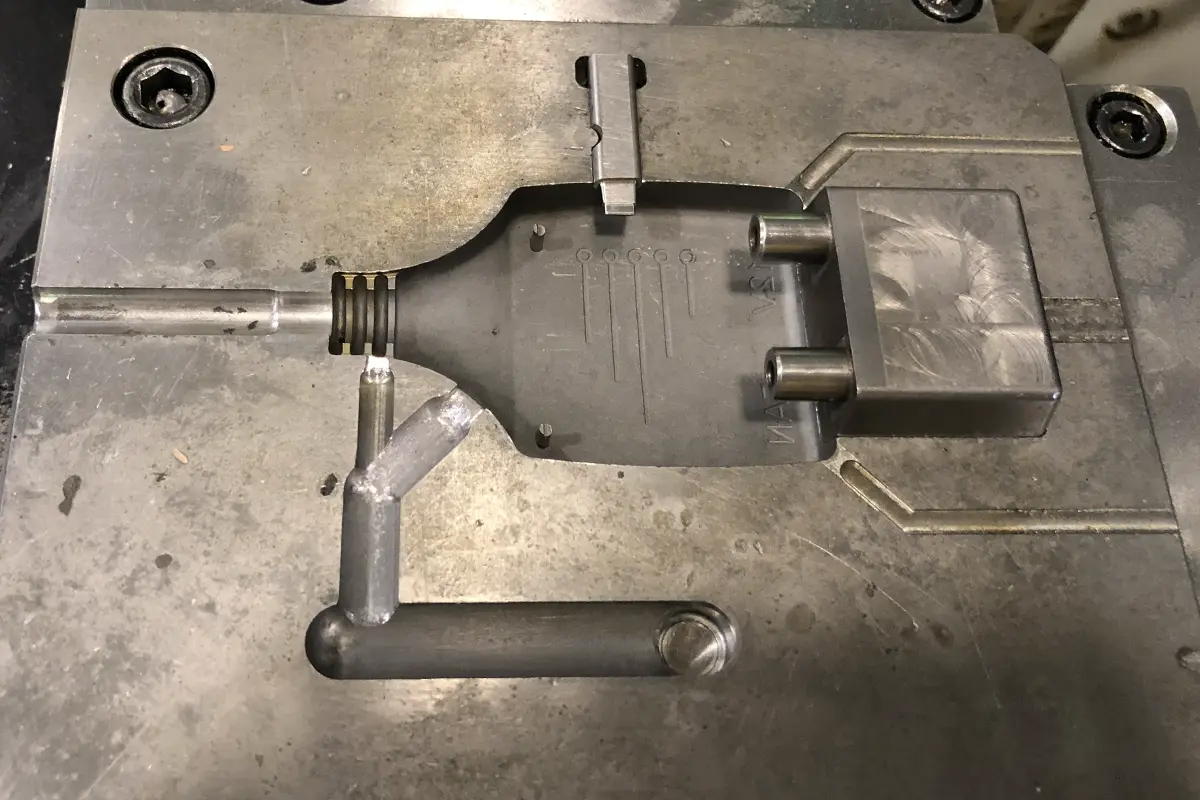
Tooling of our Drive Fan Control Cable: in this process, we supply Tri-V with the completed circuit boards, which they encase with injection molding.
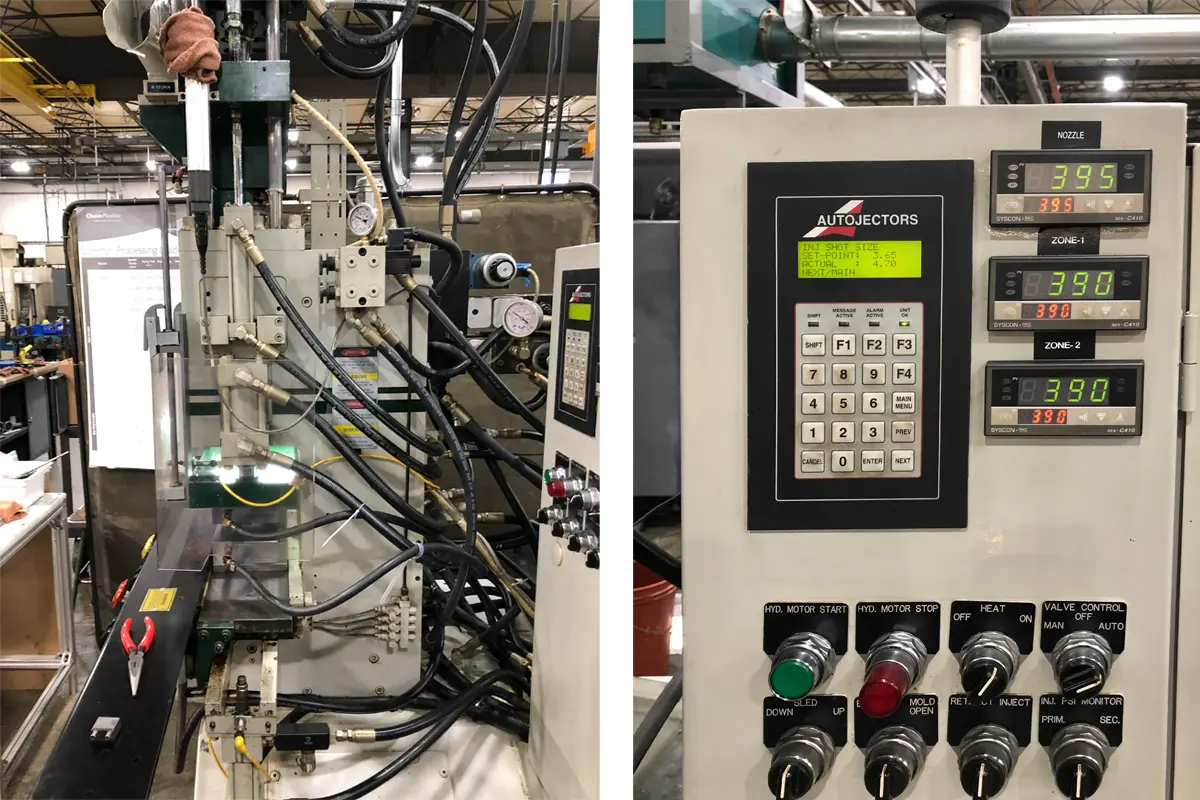
The Autojector injection molding machine at Tri-V Mfg. used to make some of FireBoard’s cases and accessories.
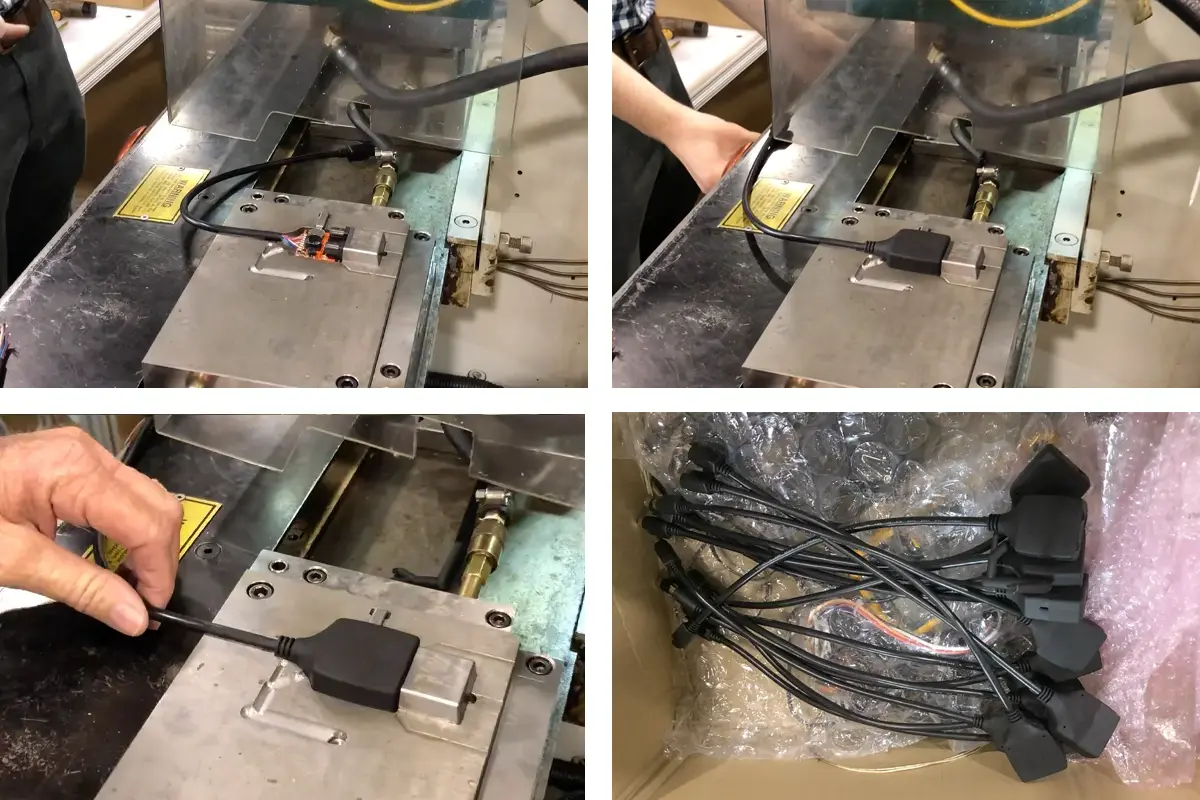
Process of over-molding the FireBoard Drive Fan Control cable at Tri-V Mfg. plug end of our dive control cable.
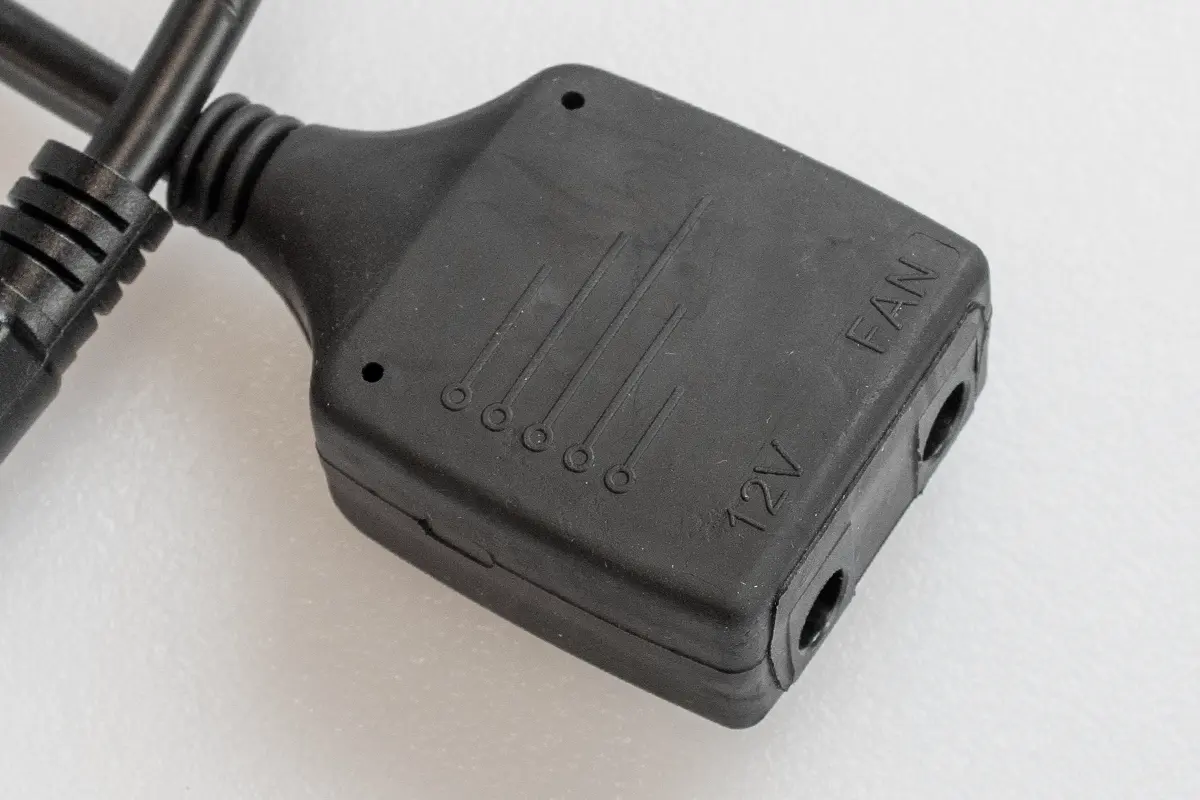
Finished injection molded plug of FireBoard’s Drive Fan Control cable used to retrofit FireBoards not built with an onboard fan connection. (i.e. FBX2 and FBX11)
Vertical Integration
In the spirit of achieving greater vertical integration, we have been analyzing the pros and cons of bringing machining and injection molding in-house. Since neither of these operations are trivial, we are carefully considering all the factors involved with bringing these in-house. Achieving the ability to run our own production plastics would ensure another large component critical to our supply chain can be reliably and efficiently produced. Going a step further towards building an in-house tool shop is even more ambitious, however if achieved, could dramatically enhance our ability to rapidly create critical tools for our operation. We’ll keep everyone posted on our progress …
Leave a reply