Manufacturing
How FireBoard Manufactures the Drive Blower
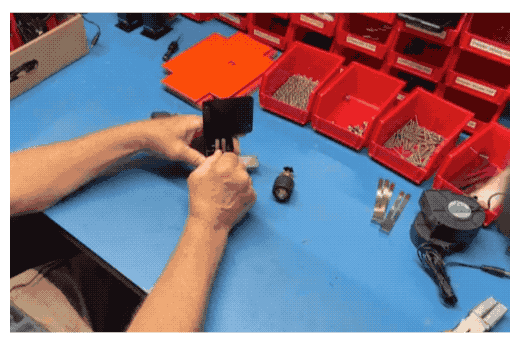
Mike assembled the blower components, an accessory that can regulate the temperature of wood or charcoal-fired BBQ grills and smokers.
The assembly floor is abuzz today at FireBoard HQ as the next batch of Drive Blower 20 CFM go into production. This small squirrel cage fan, along with a FireBoard thermometer, is used to systematically stoke the pit of wood or charcoal-fired barbecues (click here to see a previous blog post showing one of these fans being used to start charcoal on a Primo Kamado). Yet another one of their products was designed and assembled by FireBoard in KC, MO. It’s all hands on deck for a group effort to build the next batch of Drive Blowers to replenish stock.
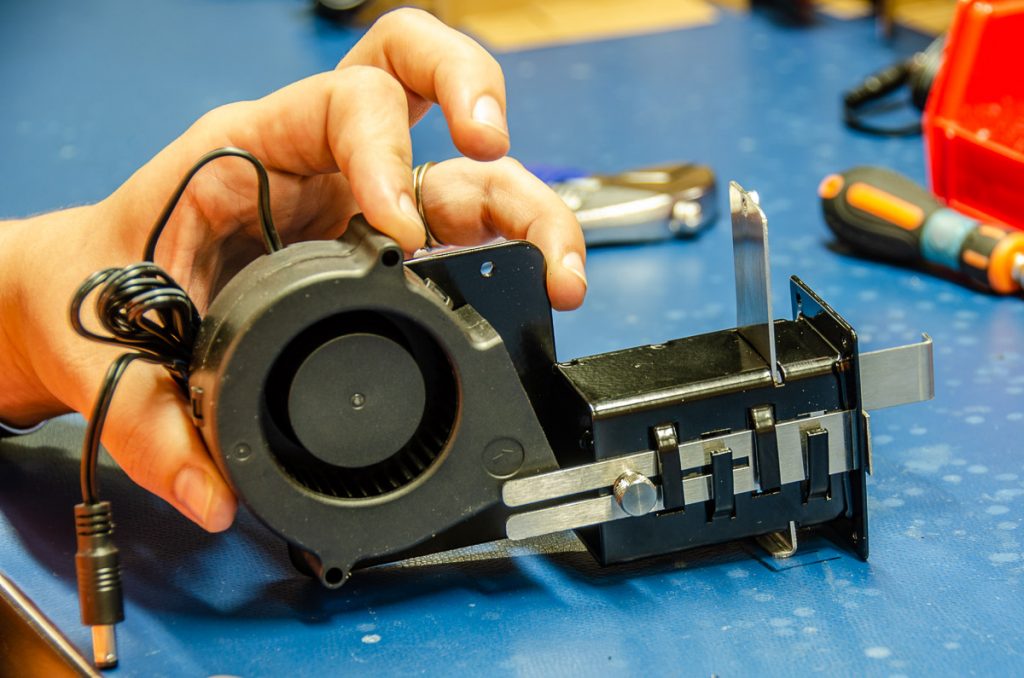
Wendy mounts the fan to the cage of the FireBoard Drive Blower.
This product is assembled by FireBoard in Kansas City, Missouri, from components purpose-built to spec. M3 Fabrication in Iowa has been entrusted to create the sheet metal components.
M3 Fabrication
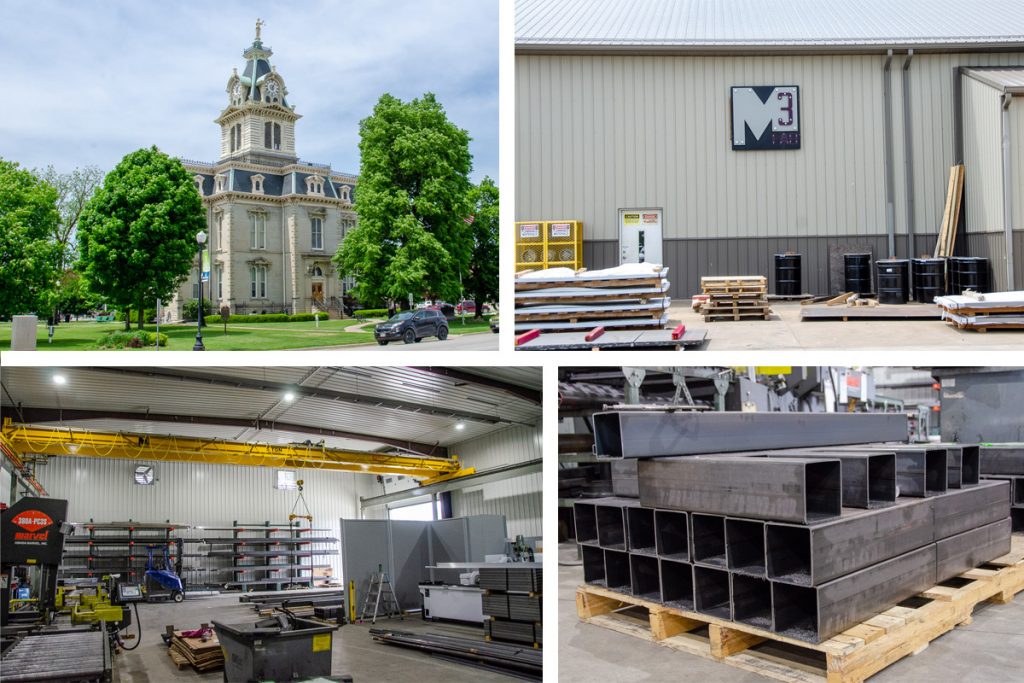
Located in Broomfield Iowa, M3 Fabrication creates components for FireBoard Labs to assemble into their Drive Blower.
Located in Broomfield, Iowa M3 is the metal fabrication workshop that FireBoard has contracted to make the housing of their Drive Blower. While they have been making this critical component for over two years, Sam and M3 have more recently created a custom staircase for FireBoard’s future headquarters.
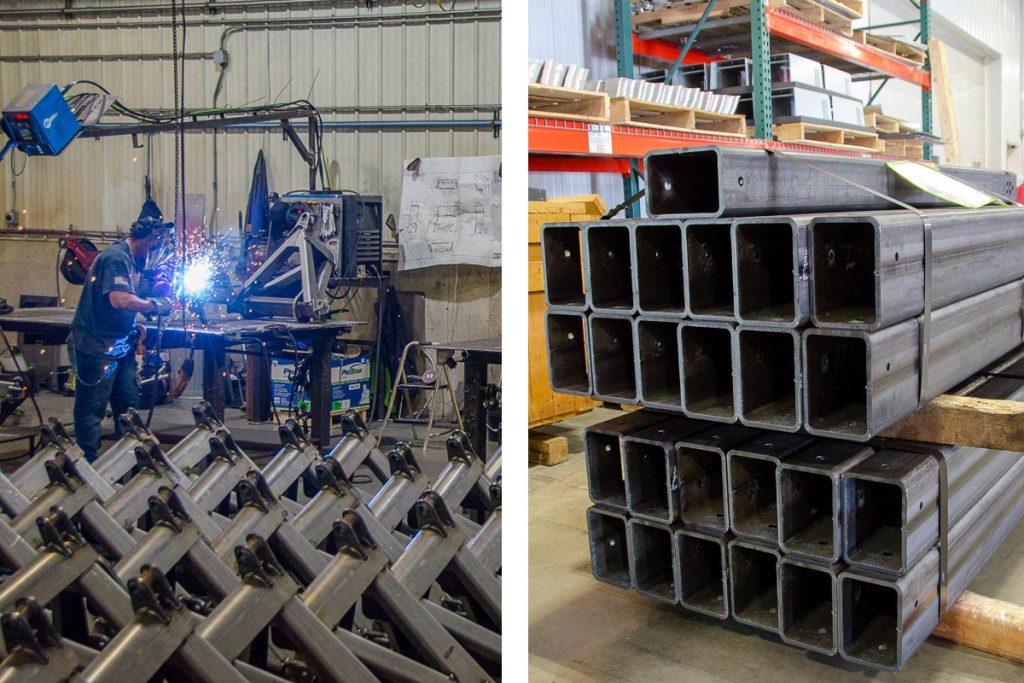
M3 takes on a wide range of jobs. FireBoard’s Blower cages are of the smaller items. Others include industrial snow plow brackets as seen here, and pop-up campers.
M3 is an awe-inspiring display of manufacturing technology for enthusiasts and professionals alike. But hi-tech machines are not the only cutting-edge element of their business. Efficiency is just as important to Sam as technology is. His workstations are organized, making it easy to see the flow of materials in, while also watching the fabricated products moving out. Also, workstations use software that continuously analyzes their jobs and materials, optimizing every cut. This ensures they are getting every usable piece out of their metal stock, minimizing wasted material.
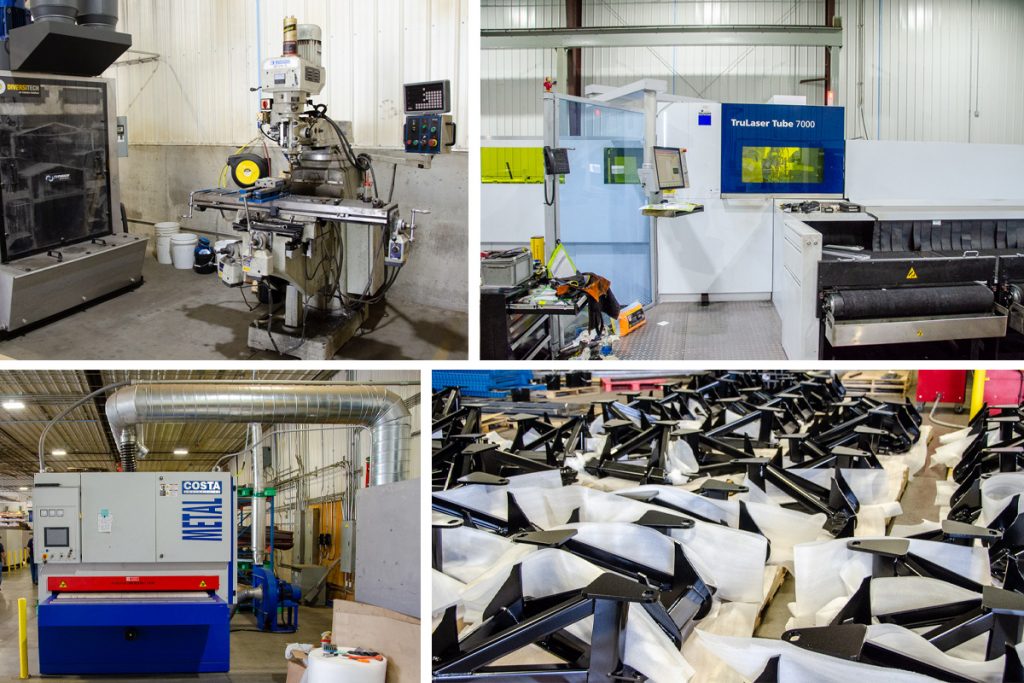
Impressions from a shop visit at M3 Fabrication: technology, efficiency and an orderly shop.
Site Visit to M3
Earlier this year FireBoard CEO Ted Conrad visited the M3 works for a tour. As luck would have it, they were in the process of producing a batch of cages, prongs and plates that FireBoard use to assemble the Drive Blower.
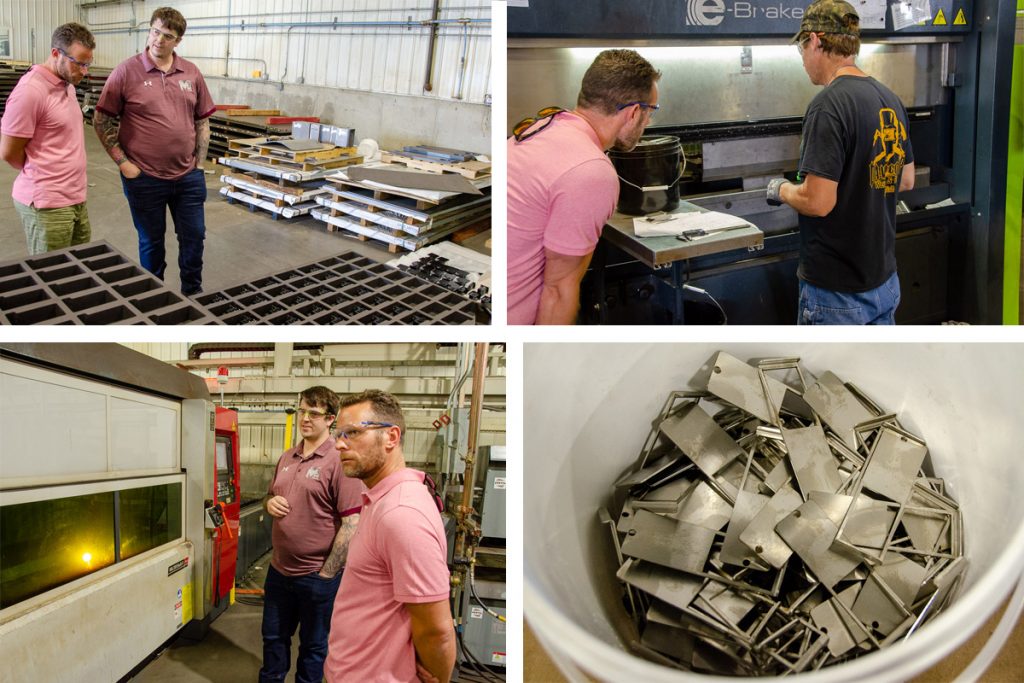
Sam McClure gives FireBoard CEO Ted Conrad a tour of M3 Fabrication bucket damper doors waiting to be installed into Blower cages.
To organize the job, the components are loaded into custom 40”x48” foam rubber trays that stack neatly onto a pallet. The story behind how these came into play is an interesting one that FireBoard Purchasing Manager Hannah Warren tells “Originally each cage was in an individual box, and then boxed in a larger box and shipped through FedEx. We realized the process was causing us and M3 additional labor costs to pack and unpack aside from the sheer material cost of the boxes. It was very wasteful especially since that cardboard was used once and trashed after we received it. We played with the idea of sending cardboard back to them for reuse on the next shipment or devising a cardboard divider for the larger box, but neither was ideal.”
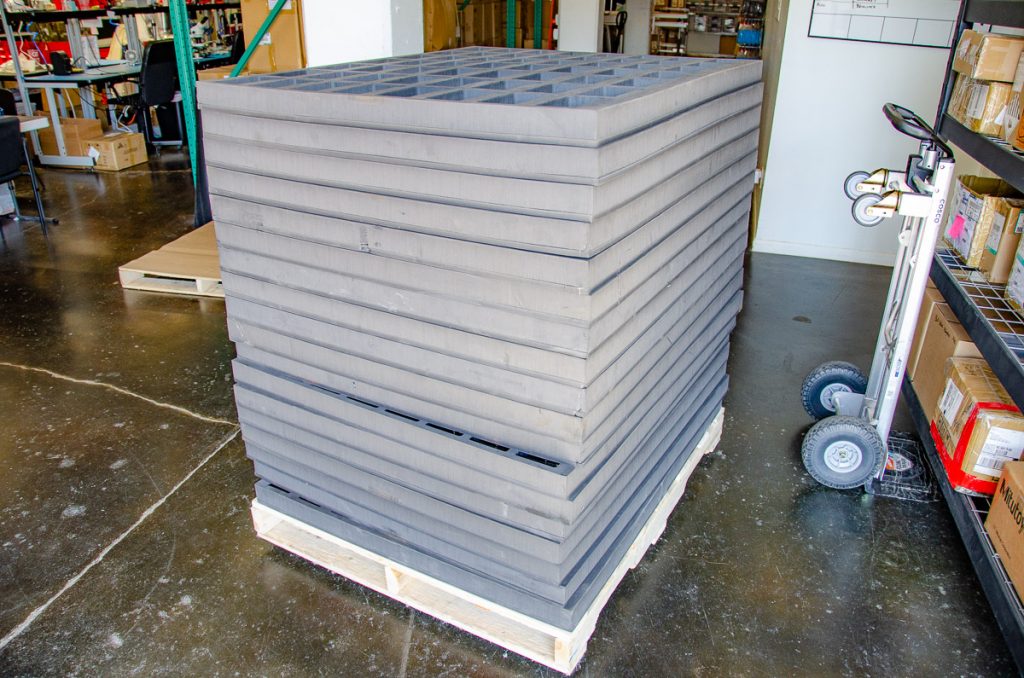
M3 ships Drive Blower components to FireBoard Labs by the pallet, in these custom rubber stacking trays, making shipping and receiving the units highly organized.
Warren goes on to explain that “Sam at M3 suggested these ingenious foam pads. Strong enough to support the metal cages and hold up during transport, but soft enough to prevent part or paint damage. They were designed to fit on a standard pallet, which would make LTL freight even cheaper than shipping them in boxes as parcels.”
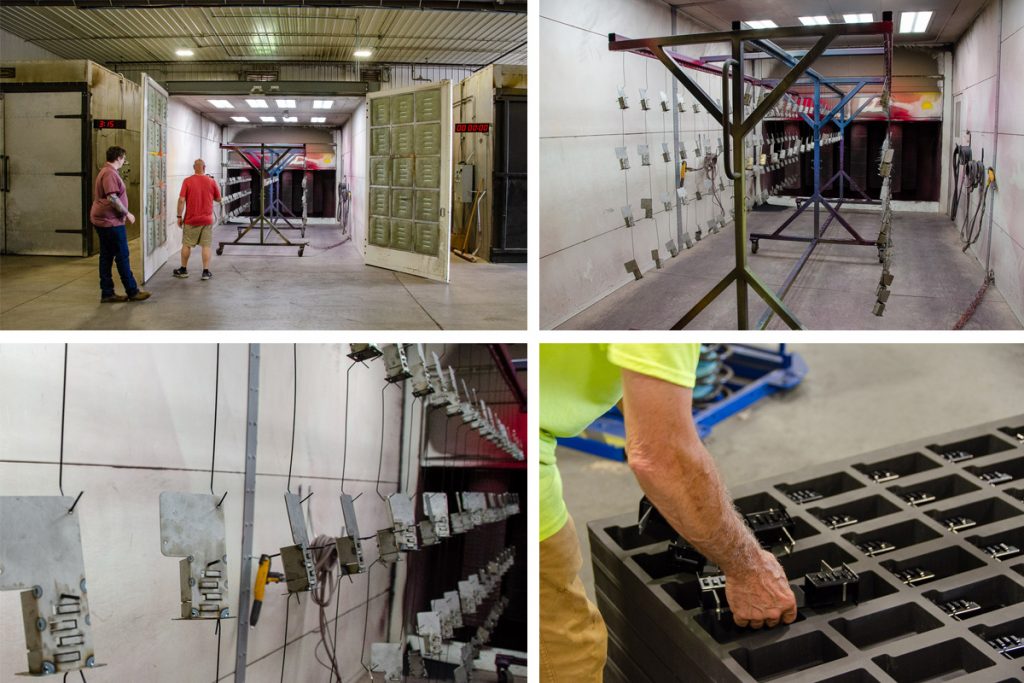
The FireBoard Blower Drive cages are in the process of being powder coated at M3 Fabrication.
Back at FireBoard HQ, the assembly team will have assembled a little over 1,000 Blowers in less than two days. This includes boxing them up in their signature red packaging; ready for distribution. Models capable of controlling this fan include the FireBoard Drive, and Pro. Owners of FireBoard 2 and the original FireBoard can control the Drive Blower with the addition of the Drive Fan Control Cable.
Look for more on Sam and M3 in future posts about FireBoard’s renovation of a former root beer bottling plant.
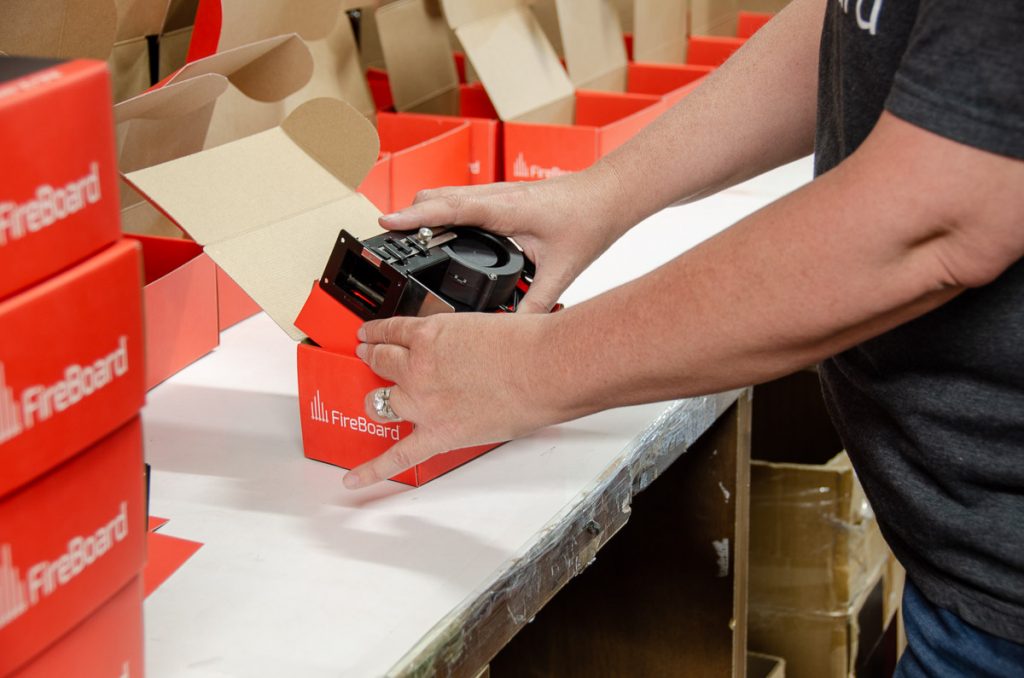
Leslie performs final quality control checks and packages the Drive Blowers ready for sale.
Leave a reply