Company News, Manufacturing, Tech, Using your FireBoard
Meet the New Drive Blower G3, Available Now
Today, we’re excited to share details about the all-new Drive Blower G3, an upgraded version of our Drive Blower model. This new blower features significant improvements in both design and functionality. At the heart of our decision to upgrade was a commitment to innovation, efficiency, and listening to the needs of our customers. As a result, we’ve designed a more durable, user-friendly, and adaptable blower that can be applied to a broader range of grills.
We’ll get into all the gritty details in this post, but some major changes include:
- All brushed stainless steel construction, replacing the old powder-coated carbon steel for superior rust resistance.
- New stainless steel braided power cable, adding durability and reliability.
- Improved plastic fan housing—now more heat-resistant than before.
- The new cover adds weather and heat resistance with a nylon-glass-filled material.
- New and improved adapter plates can be broken into sections and rotated, allowing for multiple configurations per plate.
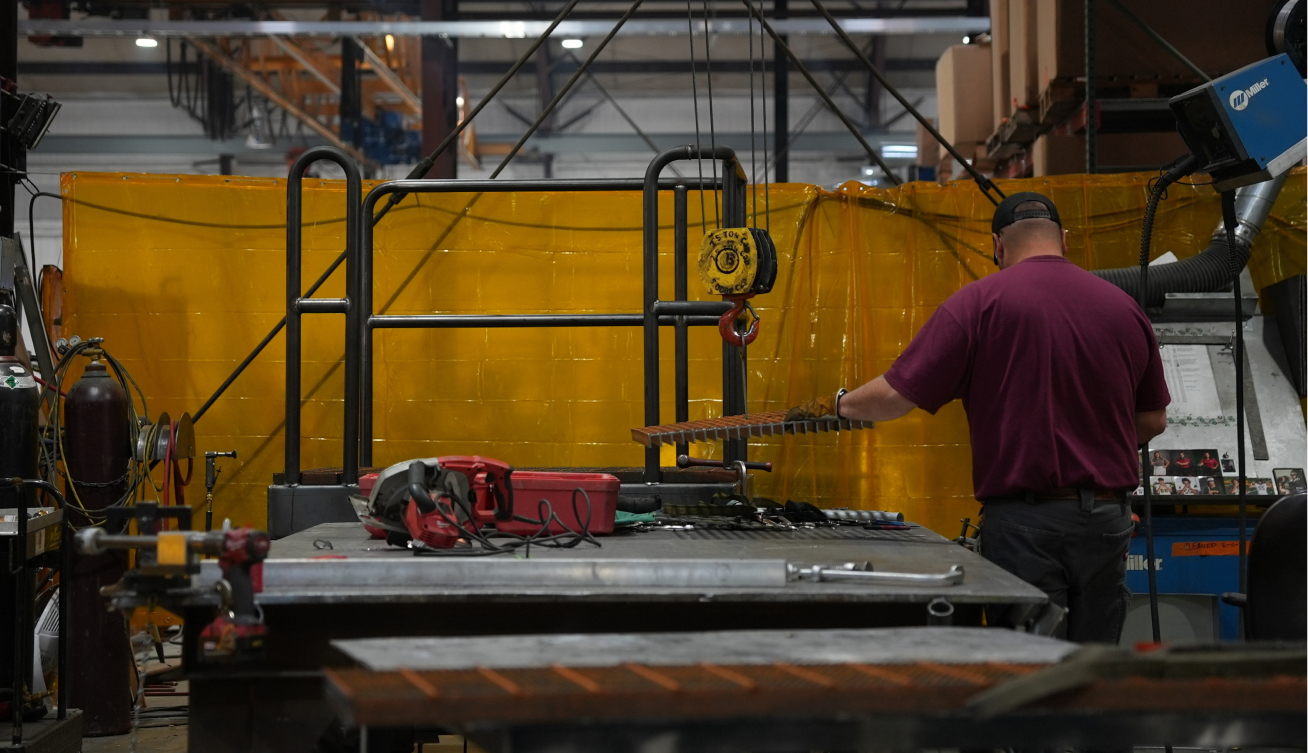
Why We Made the Switch
When we set out to design the Drive Blower G3, we knew we could make significant improvements to our old model. Through this process, we also found a great local partner in AT Industries, a metal shop here in Kansas City. This collaboration not only helped us to streamline the manufacturing process but also allowed us to produce parts with quicker turnaround times.
In addition to a more efficient process, we also had the opportunity to reflect on several limitations of the old model. For example, carbon steel components, though powder-coated, could still rust if the surface was nicked. By switching to stainless steel, we’ve eliminated that issue. Stainless steel ensures that the blower will withstand outdoor conditions without rusting—even in permanent mounting situations. To further fortify this new blower against the elements, the new fan cover is composed of a nylon-glass-filled material, which is better at keeping out moisture and debris. We even updated the power cable with a stainless steel braided design.
Updates like these were heavily influenced by the feedback we’ve gathered from our users over the years, and their insights were pivotal in shaping the new design. We knew that by focusing on better materials and a more efficient design, we could increase product quality and decrease production lead times.
“We can move faster through development and get things to market quicker than larger companies. I’m a development team of one, so I can work through the design, engineering, and manufacturing all at the same time rather than kick it around from desk to desk for sign-off between many managers.”
– Paul Skelton, Director of Product Design & Development
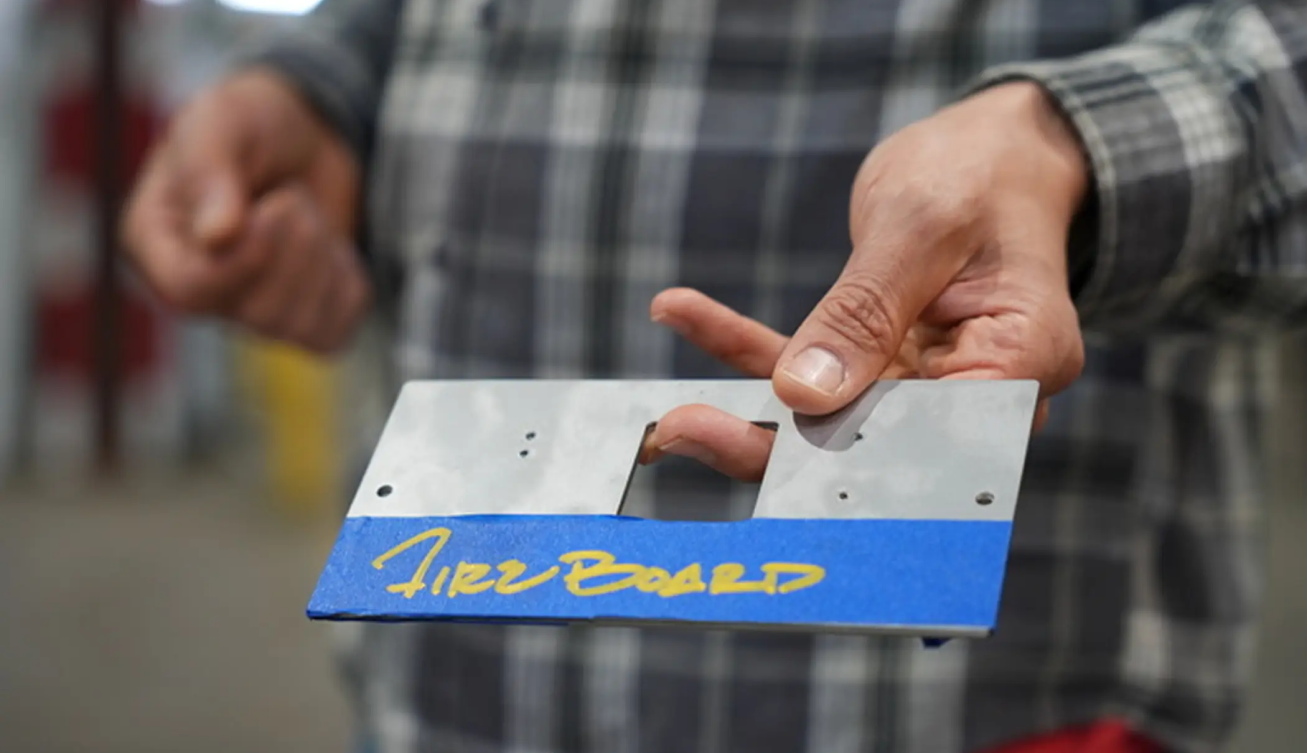
A Major Leap for our Manufacturing Process
One of the biggest changes in the Drive Blower G3 is the simplified design of the metal cage. In the old model, the process was far more labor-intensive. The prongs were stamped, requiring a custom mold. Each piece needed to be welded by hand, and the final step involved powder coating the parts—a process similar to dry spray painting but baked on for durability.
Now, with the G3, we’ve eliminated the need for welding and custom tooling. The new cage uses a simple laser-cut and bend process, which saves both time and labor. By integrating the prong track inside the tube, we’ve eliminated potential air leakage and improved efficiency. The rotating level-style damper is a new addition that further reduces air loss, replacing the less efficient trapdoor or sliding door feature from the old model.
With the powder coating process no longer necessary, we’ve significantly reduced the steps required for production. Previously, the process involved metal laser cutting, stamping prongs, bending metals, welding it all together, applying the powder coating, and, finally, shipping it to us. Now, it’s just laser cutting and bending—a significant improvement in efficiency. With fewer steps involved, we’re able to achieve tighter tolerances and better overall quality control.
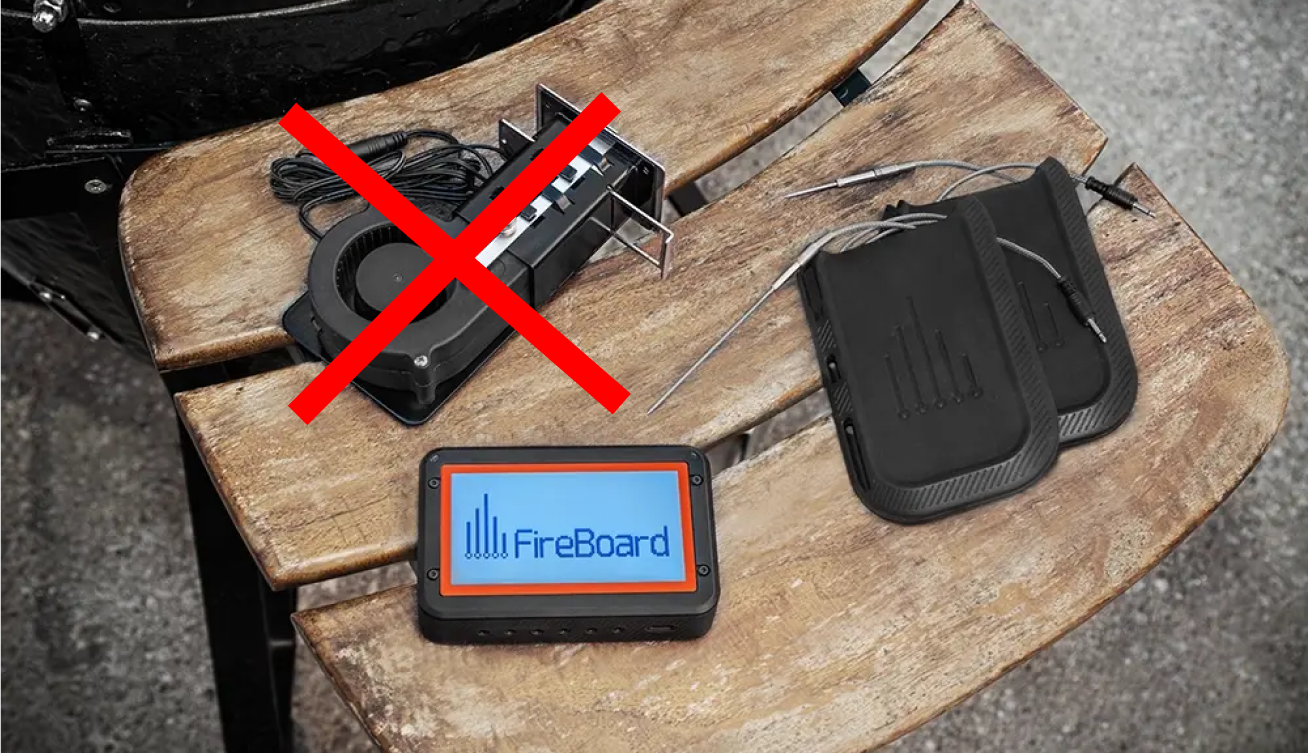
How This Affects Your Setup
If you own the original Drive blower model, don’t worry – it will continue to work just fine and it’s still supported. Once we run out of our remaining models, though, we will be switching over to the G3 model as the default blower (this will also be reflected in the FireBoard 2 Drive Bundle.)
As far as adapters go, the Drive Nozzle Adapter is compatible with both old and new models. The Ball Valve Adapter for the old model, however, is not compatible with the new G3 blower. So if you’re looking to upgrade, we recommend picking up the G3 Ball Valve Adapter for a perfect fit.
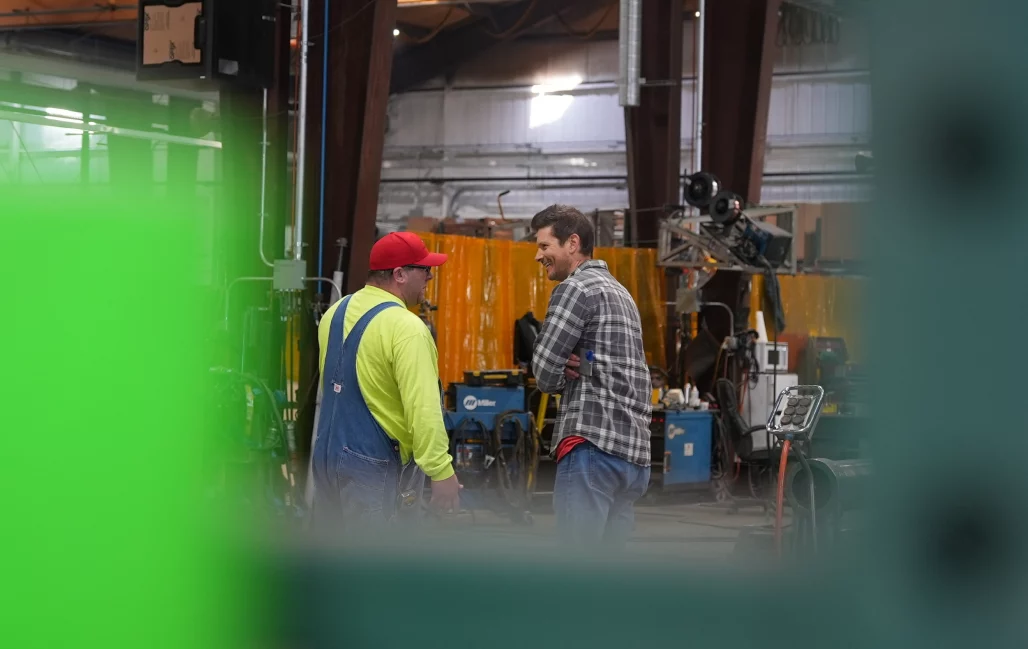
Local Manufacturing Here in KC
The Drive Blower G3 is proudly manufactured in Kansas City by AT Industries, a metal shop we discovered through a referral from another trusted partner. Working with AT Industries has been a fantastic experience. Their expertise in prototyping allows us to iterate through design ideas quickly, which has been invaluable.
Beyond the Drive Blower G3, we’ve also worked with them on several other projects, including the new G3 Ball Valve Adapter and various other components still in development. Collaborating with a local manufacturer not only supports the Kansas City economy but also allows us to maintain tight control over quality and turnaround times.
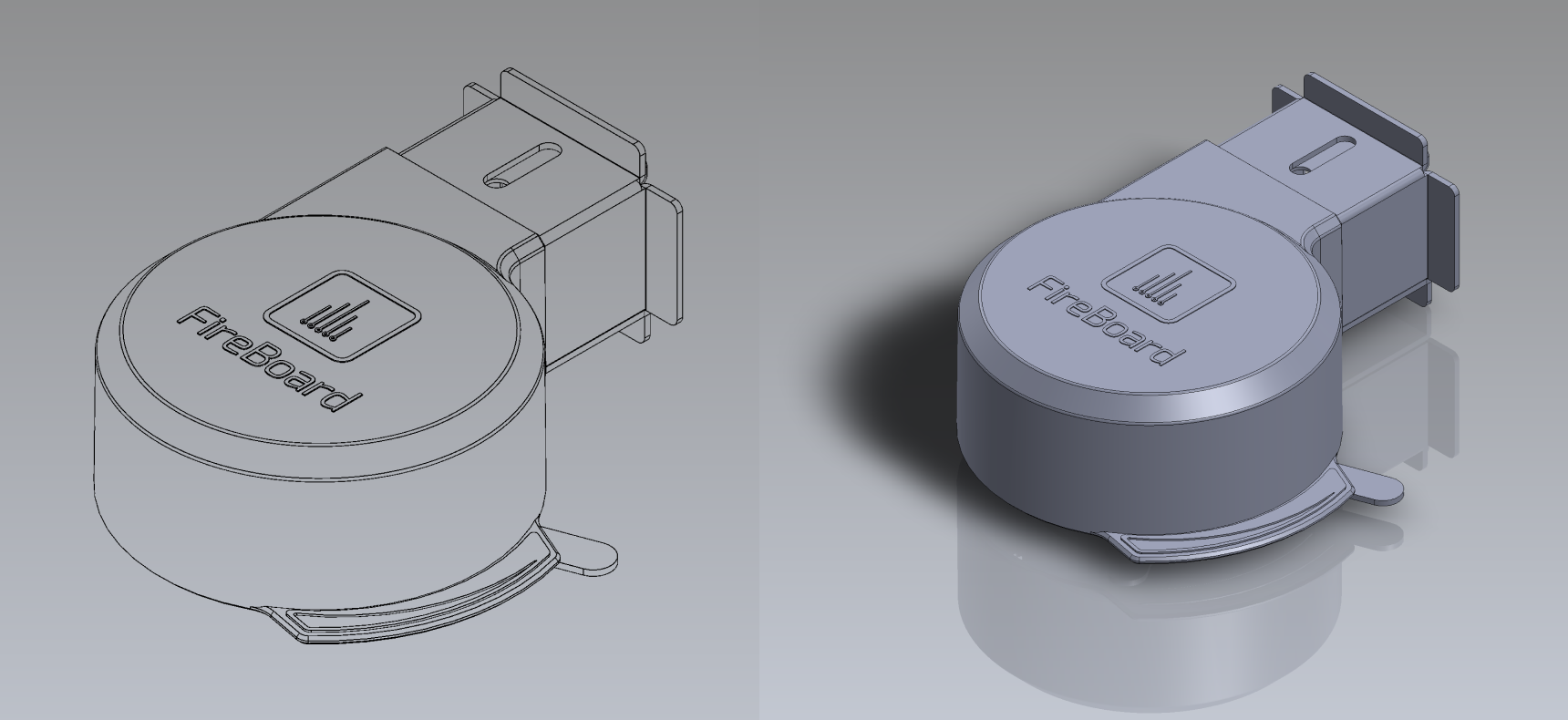
The Drive Blower G3 brings significant improvements in both durability and efficiency. With upgrades like brushed stainless steel construction, extra heat-resistant fan housing, and versatile adapter plates, the G3 is designed for better performance across a broader range of grills. Streamlined manufacturing, thanks to our local partnership with AT Industries, has also helped us reduce costs while improving quality.
Whether upgrading or purchasing for the first time, the Drive Blower G3 offers enhanced reliability and functionality to elevate your grilling experience. We can’t wait for you to try it out!
Leave a reply