Meet the Team, Process, Tech
Power of Purchasing
There are almost 200 parts and components in just a single FireBoard thermometer. Along with our other products, we are dealing with hundreds of thousands of parts working their way through our production floor. From microprocessors to shipping boxes, there is a constant stream of materials coming into our headquarters in Kansas City that allows us to build our products for consumers. Who is in charge of procuring so many parts? That’s where Hannah comes in.
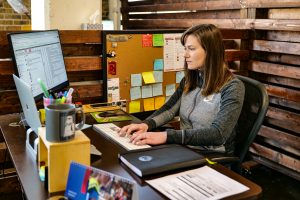
Making sure everything is ordered and on time.
“I check on inventory levels, burn rates, and what items are nearing reorder,” says Hannah, who has been in charge of purchasing for over a year. She is constantly checking and double checking inventory, ensuring that production has everything they need to keep manufacturing our products. We break down our manufacturing to “builds”. Builds are a batch of a planned quantity of product we are going to build. “I forecast about 6 months of when we will do SMT(Surface Mount Technology), THT(Through-Hole Technology), final assembly, and kitting of all our products.” Based on the “Build” schedule, Hannah is able to plan orders of all the required materials.
“A big part of my role is communication with manufacturers,” says Hannah. She is in constant contact to make sure our orders are correct and will be here in time. Hannah follows up on half a dozen projects daily, so there is a lot of multitasking and a lot of emails. The purchasing processing begins with getting quotes to set prices and MOQs(minimum order quantity). Then a PO(purchase order) is submitted with an agreed time frame when the part/component will be finished.
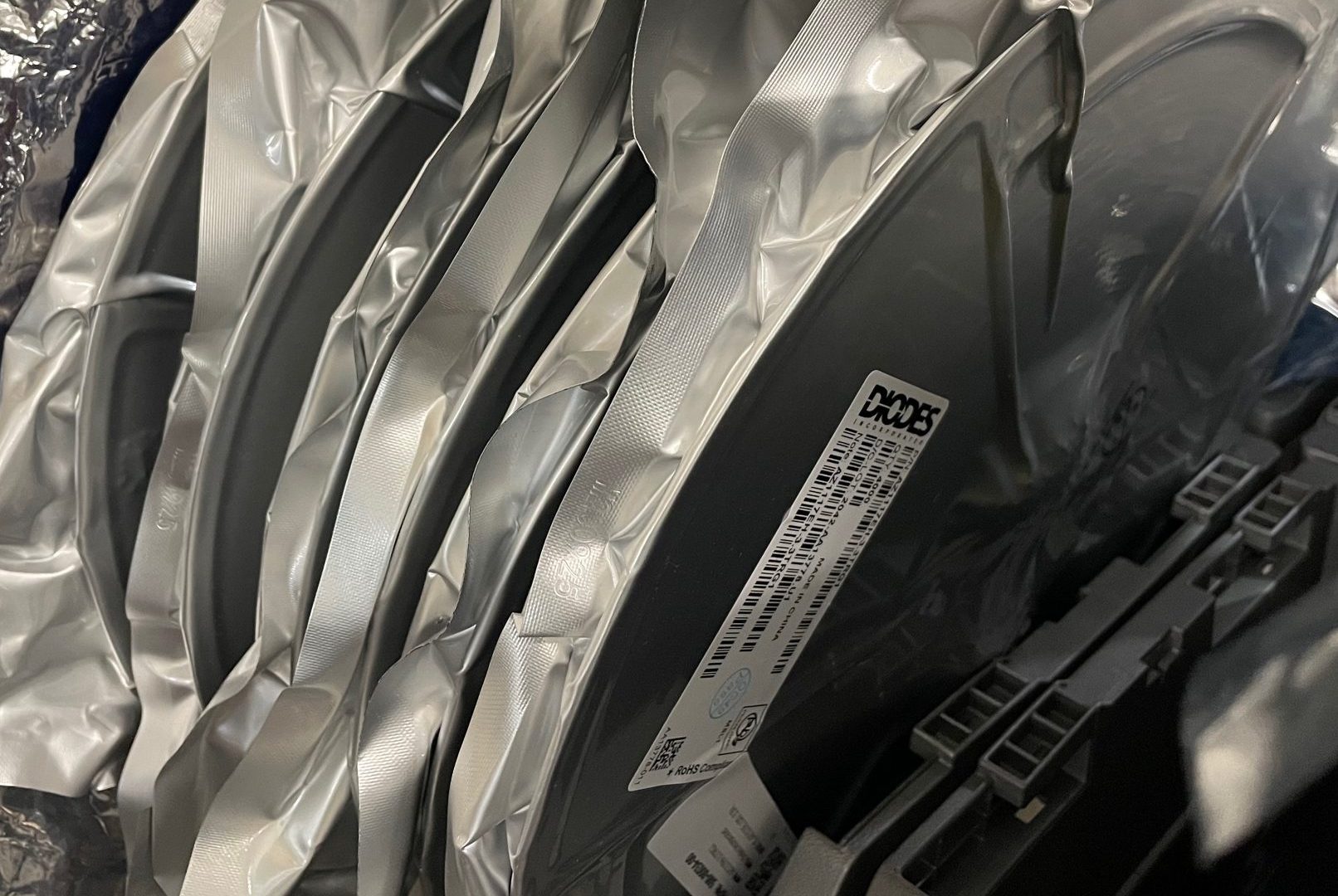
New vacuumed packed reels of parts, ready for future builds.
Some components come from overseas are shipped via ocean transport. Those have to be arranged one month in advance for pickup. Transit will then take two months, so everything has to be planned so far ahead. “I aggressively follow up with the manufacturers so delivery dates are met on time,” says Hannah. If a manufacturer isn’t able to meet our deadline, then the entire schedule needs to be adjusted.
On top of a tight schedule, there has been an electronic components shortage in early 2021 that has setback rapidly growing demand, caused mainly by imbalances from the pandemic. Orders and production are still going strong, but there aren’t enough parts to go around. “Purchasing has become a high stakes dance,” says Hannah. With extreme lead times on components jumping from 12 weeks to 50 weeks, we have had to anticipate our usage earlier than ever before and order accordingly.
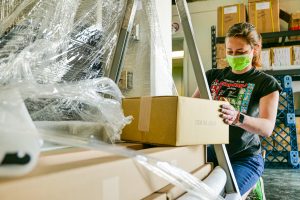
In addition to parts and components, Hannah also purchases items for the manufacturing floor like new workstations.
Once everything has been received, Hannah will go through and verify the orders making sure everything is correct. She will then update our inventory system and put the parts away until they are ready for manufacturing. Then she will repeat the process again once those parts start running low. Now do that with other parts/components we have in all of our different products.
“It might be stressful” says Hannah, “but I enjoy knowing that I am responsible for every part that goes into our amazing products and that is why I enjoy being in charge of purchasing.”
Leave a reply